HOT TAKE | Are You Training Your Employees on LOTO the Right Way?
HOT TAKE | Employee Turnover, a Nightmare for LOTO
21 May 2024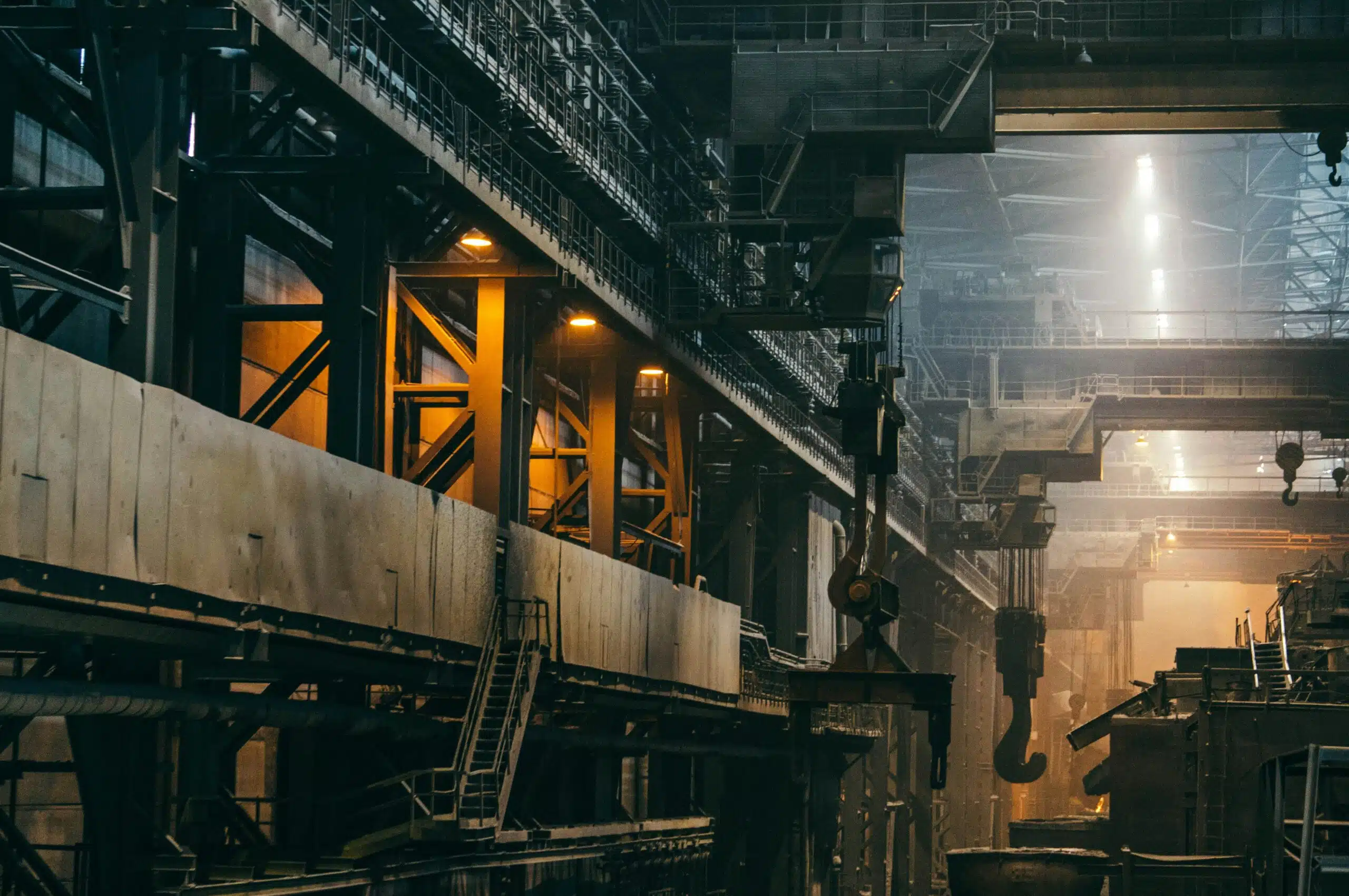
Hot Take on the LOTO Chaos Employee Turnover Brings
Employee turnover is a nightmare that is here to stay, so good luck with your LOTO! Lockout Tagout is fundamental in mill safety and with so many transformations in the industry it is vital that the basis for such safety is as stable as bedrock. With the next generation of paper makers on our heels, there is an urgency in eliminating Lockout Tagout bad habits. We have heard it 100 times over the last decade at CONFORMiT, “We had a great LOTO system which this one guy was maintaining, but when he left for retirement, we could no longer maintain the same level of quality or efficiency.”
The underlying problem of employee turnover is always the same –
- Systems rely too heavily on a single employee’s personal knowledge
- Expectations are skewed, thinking that humans will document procedures with consistency
Referring to repeatability in a manufacturing process, a client once told me, “If you want to be certain something is never done twice the same way, ask a human to do it.” This truly pinpoints the issue of when LOTO responsibilities change hands.
For example, a typical mill might have just shy of 1000 pieces of machinery and north of 3000 individual energy isolating devices (such as manual valves, breakers, and so on). Each procedure can reference tens of these individual energy isolating devices, and each can also be found on tens of individual Energy Control Procedures (ECP). The people assigned to the LOTO system maintenance are expected to know where each device is used and remember to update each individual ECP accordingly. While well-named components and updates are ideal, experience teaches us that not only is an individual valve assigned a variety of names within different procedures, but there is no consistency or continuity within each ECP where the valve is used.
Take this poorly managed but memorized process, physically housed in the mind of one employee, and imagine what happens when he leaves his position. No amount of trade off will accurately transfer that information, nor will it set the next employee up for success. They will most likely in turn devise their own memorized system of chaos, leaving everyone at risk which literally translates to the employee turnover LOTO nightmare.
The worst case we saw was in a mill where this problem forced them to redo 100% of their ECPs. This redo cost them 3500 man-hours – almost 2 years’ worth of work – to rebuild every single ECP from scratch, all because no one was confident that the data in the old ones were actually accurate. What’s terrible about this situation is not even the number of man-hours spent, seemingly small when you consider there are 800 employees in that facility. What is truly terrible is that their system was only a couple of years old. So that meant they spent 2 years worth of work redoing a process that had only lasted 4 years total. A LOTO system when created and maintained with care and using the right tools is built to last.
Although this is the worst case scenario, there is a consistency of smaller-scale examples just like that. There is only way to prevent that kind of chaos.
There are two steps you must consider to eliminate the nightmare of LOTO chaos, that stems from employee turnover.
1. Build a list of individual energy isolating devices, which should include:
- Device unique ID
- Device description
- Device energy and magnitude
- Device location
- List of ECPs, in which device is used
- Materials required, to install padlock on said device
2. Build each individual ECP, copying information from the list of devices.
There are many tools that allow you to achieve success in this area, with more or less effort. The key to a successful handover and ultimately maintaining a high bar for Health & Safety lies with the decisions you make in selecting such a tool. A tool that is customized to the needs and habits of your employees, that takes into account every aspect – from energy isolating devices to ECPs and beyond. While the nightmare of employee turnover is here to stay, you can remedy the chaos. Safety isn’t an isolated issue and neither is the legacy you leave behind as the new generation of paper makers take over.
Did we miss something? We’ve seen a lot in our 35+ years of working to protect those in the Paper Industry. That said, we are open to any opportunity to gain another perspective – so, feel free to reach out and teach us something new. Your voice is one we want to hear!
About CONFORMiT
For 35 years, CONFORMiT has developed and marketed Cloud-Based Software-as-a-Service products to analyze and manage environmental, social, and governance (ESG) risks to support sustainability strategies. CONFORMiT’s simple and reliable solutions also promote companies’ and workers’ excellence in occupational health and safety management.
CONFORMiT enables its clients and their communities to provide a healthy and safe workplace while improving their productivity and profitability to build a more sustainable future.
For more information: www.conformit.com