The Heart of Pulp and Paper | The Communities
Can you Prevent Downtime in your Paper Mill?
25 October 2024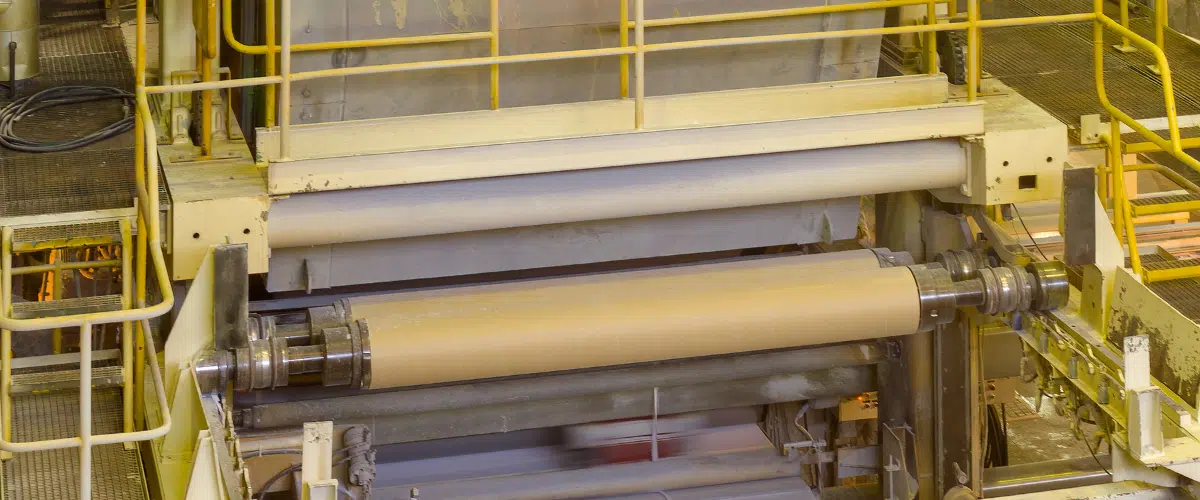
Can you prevent downtime in your paper mill? Well, nothing is certain except death and taxes…and machine downtime. The reality of downtime for a paper mill is nothing new. It’s a staple for any industrial manufacturer, a natural consequence of the maintenance needed on these giant, beautiful machines.
Whether production downtime is scheduled or unplanned, the process is the same:
- Shut down the machine.
- Make the machine safe for employees.
- Repair/update/improve the machine.
- Remove the safety measures.
- Put the machine back into play.
From unexpected breakdowns to routine maintenance, downtime disrupts the manufacturing process, leading to lost revenue and decreased efficiency. However, by focusing on reducing chaos and enhancing your processes, managers can take significant strides in minimizing downtime and improving overall operational efficiency.
So, in short, while you cannot prevent downtime in your paper mill, there are certainly ways to reduce it.
UNDERSTANDING THE IMPACT OF DOWNTIME
Minimize Downtime to Boost Productivity
Downtime can arise from various sources, including equipment failures, maintenance activities, and operational inefficiencies. The impact of downtime is far-reaching, affecting not only production schedules but also labor costs, customer satisfaction, and the bottom line. According to a study by the International Society of Automation, manufacturing downtime can cost companies as much as 20% of their productive capacity. For paper mills, this translates into substantial financial losses, highlighting the critical need to minimize downtime and maintain seamless operations.
Prevent Downtime with Proactive Measures
Preventing downtime requires a proactive approach that involves regular maintenance, employee training, and the implementation of effective systems. By adopting strategies that focus on preventing machine downtime, mills can reduce the frequency of disruptions and ensure that production runs smoothly. One effective measure is the use of predictive maintenance techniques, which involve monitoring equipment performance and identifying potential issues before they lead to failures. This approach allows for timely interventions, reducing the likelihood of unexpected breakdowns and minimizing manufacturing downtime.
For example | After experiencing a digester mechanical failure, one Canadian paper mill this fall was forced to shut down their NBHK production for more than two weeks. This resulted in an estimated loss of 45, 000 tonnes of pulp in that short period of time.
We know that when it comes to mills, especially those that run 24/7, every second of production counts. Ensuring you are on the top of your maintenance game is essential.
THE ROLE OF LOCKOUT TAGOUT
Ensuring Safety and Compliance
Lockout Tagout (LOTO) procedures are critical for ensuring the safety of employees and compliance with regulatory requirements. These procedures involve the isolation and securing of energy sources during maintenance or repair activities, preventing accidental startup and protecting workers from hazardous energy. In paper mills, where heavy machinery and complex systems are prevalent, effective LOTO procedures are essential for preventing accidents and minimizing downtime.
LOTO is the main way to keep mills safe and compliant. Without proper systems in place, sufficient training, and the right tools at hand, unwanted events can result in hundreds of thousands of dollars in fines, weeks of downtime as investigations are carried out and, worst of all, serious injuries and fatalities (SIFs) that have tragic impact on your community.
As mentioned at the opening of this article, the process of LOTO is pretty much standard. While you know Energy Control Procedures (ECPs) keep workers safe, you may not have considered how bettering your LOTO system can actually maximize your production and revenue!
Implementing Robust ECPs
To maximize the benefits of ECPs, Operations and EHS managers should focus on several key areas. It is crucial to develop comprehensive LOTO protocols that cover all aspects of the process, from energy isolation to tagout procedures and verification steps. These protocols should be clearly communicated to all employees, and regular training sessions should be conducted to ensure that everyone understands and follows the procedures. Indicators, expected trends, and desired outcomes should be monitored to ensure proactive actions are to prevent non compliances.
When workers adhere to the procedures in place, downtime is minimized. No one is losing time running to and from lockout areas, searching frantically for physical or digital components of the Lockout, and so on. However, your workers can only do so much with the process your mill has in place. If your Lockout Tagout software or set-up isn’t up to par, your workers and ultimately your ability to maximize your output will be limited.
Regular Audits and Continuous Improvement
Yearly inspections of LOTO procedures are not only essential to identify any gaps or areas for improvement, but they are also mandatory in most jurisdictions. Mills should conduct periodic reviews of the procedures and solicit feedback from employees to identify potential issues or areas where additional training may be needed.
Let’s ask the old age question again, can you prevent downtime in your paper mill? The answer is still no, however by continuously improving LOTO procedures, paper mills can enhance safety, ensure compliance with regulatory standards, and prevent unplanned downtime (a.k.a. increase production revenue).
For example | A leader in tissue centralized their ECPs (LOTO sheets) adopting an ai-powered Lockout Tagout software. This eliminated the chaos associated to their previous system that had been running on 80% outdated procedure sheets.
IDENTIFYING THE WEAKEST LINK
Streamlining Procedures
As we just discussed, a poor LOTO system is a major contributor to unnecessary downtime. A chaotic and disorganized ECP setup – like using Word & Excel or makeshift software – can lead to operational inefficiencies and increased downtime. It’s important to review your process and optimize your system, to ensure they function seamlessly and support the overall production process.
For example | A top papermaker in the Southern United States had once employed a full-time worker, just to keep their Word & Excel ECPs updated and compliant. Once they integrated with an enterprise-level Lockout Tagout module, that employee was able to get back onto the floor and refocus energies and manpower to keeping production up and running, increasing their potential for production.
Updates and Changes to ECPs
The amount of time lost in Lockout because of incomplete or inaccurate LOTO sheets is astounding. Often, these discoveries are only made once the Lockout is in process and the authorized individual is already at the machine. The last thing you want to be doing is holding up maintenance teams and delaying reproduction because you must run back to the Lockbox room and sort through an old system of outdated ECPs.
It’s essential to maintain accurate and up-to-date documentation of all control systems, including wiring diagrams, software configurations, and hardware specifications. Implementing an intuitive and ai-powered LOTO software ensures consistency and minimizes the risk of errors.
Communication and Collaboration
Effective communication and collaboration between different teams is vital to minimize downtime in your mill. Front-line managers should facilitate regular meetings and information-sharing sessions to ensure that all relevant stakeholders are aware of any changes or updates to the control systems. This collaborative approach helps prevent misunderstandings and ensures that everyone is on the same page, ultimately reducing the likelihood of production downtime.
LESS DOWNTIME, MAXIMUM PRODUCTION
In Paper, minimizing downtime is essential for maintaining productivity and profitability. Benefit yourself and your facility and avoid looking for shortcuts to prevent downtime overall in your paper mill. By focusing on eliminating the chaos of bad Lockout Tagout procedures, mill managers can take significant strides in preventing unplanned downtime and improving overall operational efficiency.
Proactive measures such as predictive maintenance, efficient operational risk management, and robust LOTO procedures are key to achieving these goals. By implementing these strategies and continuously seeking opportunities for improvement, paper mills might not be able to prevent downtime, but they can certainly maximize efficiency, increase their production revenue, and ensure long-term success.
About CONFORMiT
For over 35 years, CONFORMiT’s Lockout Tagout system has been optimizing production, minimizing worker risks, and maximizing profits for high-risk industries across North America. Our zero-training-required, AI-powered enterprise solution frees employees from clumsy, chaotic processes. Unlocking safety excellence has never been so simple.
CONFORMiT enables its clients and their communities to provide a healthy and safe workplace while improving their productivity and profitability to build a more sustainable future.