LOTO | Different Types of Locks for Different Purposes
Health & Safety Key Performance Indicators
5 June 2018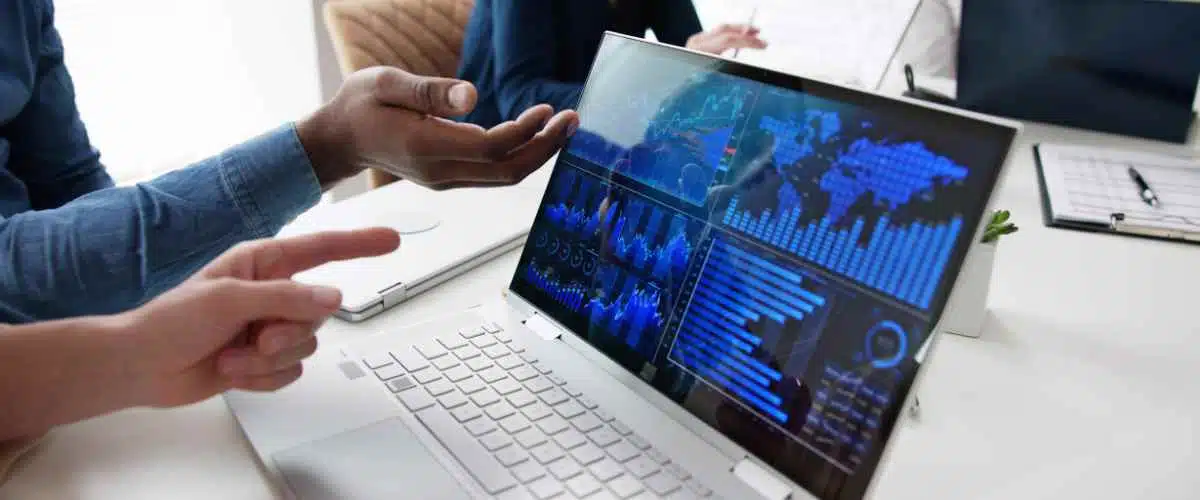
Health & Safety KPIs
What kind of statistics or reporting do you use in the workplace to measure safety? Using Health & Safety Key Performance Indicators (KPIs) correctly can optimize the insight you gather and result in more adequate improvements to the overall health and safety of your facility.
The financial cost, number, frequency, and severity of occupational accidents and disabilities, per 200,000- 1M man hours worked is an enormous amount of information. These indicators are most often limited to the financial aspects of Health & Safety and usually focused around losses. They don’t appeal to better working conditions, near misses, and so on.
Lagging Indicators
Passive management indicators are not great for evaluating the performance of your Health & Safety management system. In fact, they only indicate whether or not your efforts in the past have been fruitful or if you have been lucky. They are incapable of telling you if your preventive system functions well or if all the required elements are in place to obtain clean data. With such lagging indicators, you will not be able to identify where you have fallen short, and in turn you will continue to repeat the same mistakes.
Leading Indicators
It is increasingly important to invest in indicators that actually provide insight on Health & Safety management and on adherence to preventive measures. For example,
- The % of completion of planned activities such as inspections, preventive maintenance of equipment, worksite safety meetings, etc.
- The % of rectification of non-compliance detected during these activities.
- The % of implementation of Corrective and Preventive Actions (CAPA)
- The % of implementation of your action plans.
- The % of training programs required legally versus the % completed.
- The % of training programs required by the organization versus the % achieved.
- The quality of reports generated following inspections and incident/accident investigations.
- The % of Occupational Health & Safety (OHS) communications released versus those planned by the supervisors and managers.
- The % of protective equipment worn and observance of safety instructions.
- The % of application of lockout during planned and unplanned maintenance tasks.
Choosing Performance Indicators that Generate Health & Safety Messages
For example, a distribution centre can present the cost of its occupational injuries in the following manner:
- Number of units per box, delivered to the customer.
In its freight operations, it could indicate:
- Number of damages sustained per 1M kilometers covered.
These numbers are clear indicators, since they deal with a certain facet of the organization’s mission. They create a certain image in the minds of the employees and are therefore more informative.
Among significant Health & Safety indicators, we can consider the training provided at the workplace, cleanliness, and the organization of work areas. It is also possible to focus on the percentage of compliance to work safety regulations, on lockout, on the operation of forklift trucks, the degree of compliance with regard to the use of personal protective equipment, and so on.
Presenting the observed results to the employees will allow them to assess whether or not they have attained the objectives. The results also identify the actions that need to be taken in order to continue the efforts related to OHS, with a view to maintain satisfactory performance. What matters is the ability to choose elements that is meaningful for the employees.
It is important to emphasize the activities that have been completed and have made the workplace safe and secure. Say, for example, that 78% of accident investigation and analysis reports have been completed in the most satisfactory manner, all worksite inspections have been conducted, and that 80% of the problems identified were resolved within the planned time frame. Highlighting these aspects will ensure that the people who carried out the preventive activities receive the recognition they deserve. It also encourages others to participate in a similar manner.
All information shared with the staff shows the importance that the organization gives to the OHS program on a daily basis. Moreover, when the scheduled Health & Safety actions are clearly indicated, it has a positive influence on the company’s culture.
Occupational Health & Safety Performance Indicators
The principle objective of creating performance indicators is to provide managers, prevention specialists, and members of the Health & Safety committee with summary documents, tracking reports, with regular and systematic reporting, and a collection of indicators that are most useful for an enhanced knowledge of risks and risk management: identifying key improvement or deterioration trends over time, identifying deviations that necessitate priority plans of action, evaluating the degree of objectives attained, and comparing the organization’s data with that of the sector (benchmarking).
The implementation of an Occupational Health & Safety indicators tracking report serves both as a situation diagnostic tool, and a driving force behind actions and improvements. It is important to assess whether the planned improvements are effectively realized and whether this mechanism allows one to keep track of the progress of actions and their efficacy. This “feedback” promotes effective behaviour by measuring either the progression towards or deviance from the objective to be attained, consequently modifying the perception as well as the actions of those responsible for ensuring OH, while reducing the observed deviation.
Principles in the Development of OHS Indicators
Having an objective description that provides preventive measures is all the more important today in the field of Occupational Health & Safety, since the participants are often under emotional stress and are not in a position to calmly analyze the situation, thus favouring hasty and subjective judgments, forming fuzzy opinions in a conflicting and accusatory environment.
However, numerical indicators have an objective importance if they are precise, clear, recognized, and circulated, and if their method of production is validated, compliant, and simple. The Health & Safety status indicator should be uniform over time, consistent with other indicators so as to obtain well-monitored significant ratios that avoid deviation. The choice of indicators is a mutual decision that is taken based on a consensus between prevention specialists, Health & Safety committee experts, human resources, supervision, and management.
Only in these conditions can the indicators successfully promote the exchange of different points of view among the company managers, salaried staff and their representatives, and OHS professionals, thus helping initiate actions in the right direction. Using analysis and interpretation of Health & Safety Key Performance Indicators (KPIs), a sense of measurement can be obtained, and the useful indicator can be used to initiate action.
To design this tracking report, it is important for the organization to select some indicators that are relevant to its activities instead of creating a cumbersome statistical apparatus that is inefficient over time: it is absolutely necessary to avoid analytical deviation and the administrative stagnation that results from it, reducing the reliability of the entire system and diminishing the motivation and adherence of teams (errors, faulty and irregular entries, partial and late updates, etc.).
Different Occupational Health and Safety Indicators
Tracking reports for each sector and a consolidated summary for the organization are developed from the various operational performance indicators (number of working days lost, number of first-aid interventions, frequency rate, severity rate, etc.) and from system performance (percentage of people undergoing OHS training, percentage of preventive actions achieved, degree of progression of plans of action or of delays in relation to the scheduled time frame, percentage of OHS investments made, etc.). Other factors stem from human resources related to unpleasant working conditions (absenteeism, turnover, number of complaints, etc.).
Absolute Indicators and Relative Indicators
Derived from reports of occupational accidents and disabilities, the number of occupational accidents is the most commonly calculated value. However, this value in itself has very little significance: does a dip in this value means an improvement, if at the same time there is a reduction in staff numbers? What if this number includes a higher number of severe accidents? It is therefore essential to calculate ratios that correlate this number with other parameters, thus enabling a better estimation of the situation. For example,
Frequency rate (FR):
Number of accidents with sick leave of more than one day occurring during the annual period for every 200,000 hours or 1,000,000 man hours worked (taking into account only occupational accidents that require treatment beyond a first-aid intervention).
Severity rate (SR):
Number of days compensated for every 200,000 or 1,000,000 man hours worked.
In order to be relevant, and to allow targeted action, these indicators should be determined based on narrow segmentation: status (full time or part time), gender (men/women), age group, type of accidents (noise, musculoskeletal disorder, respiratory disorders) and so on. Such segmentation helps take into account variabilities, since the same working environment can have different effects, and it helps to detect “risk” groups that require special preventive measures.
We can distinguish between reactive indicators that are used to analyze OHS data and proactive indicators that are used as monitors to ensure that anticipatory actions are carried out (ex. number of medical visits prior to resuming work, sampling of ambient air, noise measurements, OHS training initiatives, etc.).
Trending Indicators
Trending Health & Safety Key Performance Indicators (KPIs)indicators help to keep a record of, for example, the change in the number of occupational accidents and disabilities over the years, within the same organization, by calculating the rate of progression from one year to another, or on an average over several years.
Result Measurement Indicators
These indicators show to what extent the OHS objectives have been attained, by calculating the difference in the results, in relation to the objectives set by the action plans (originating especially from plans focused on the improvement of working conditions). For example, if the objective is to reduce the frequency of occupational accidents by 10% per annum, and if such accidents have only reduced by 7%, then the difference is of 3%.
Comparative Indicators
Comparative Health & Safety Key Performance Indicators (KPIs) present corresponding data of other organizations, significant or comparable divisions, or departments and the deviations (benchmarking). These indicators enable nuanced approaches that direct actions towards real priorities. They are not biased by a narrow local vision. The use of these comparisons is, however, tricky due to the possible diversity of measurements among several organizations. Only the important differences are thus significant.
CONFORMiT can help you to conceptualize and compile your performance indicators
About CONFORMiT
For over 35 years, CONFORMiT’s Lockout Tagout system has been optimizing production, minimizing worker risks, and maximizing profits for high-risk industries across North America. Our zero-training-required, AI-powered enterprise solution frees employees from clumsy, chaotic processes. Unlocking safety excellence has never been so simple.
CONFORMiT enables its clients and their communities to provide a healthy and safe workplace while improving their productivity and profitability to build a more sustainable future.