LOTO | Different Types of Locks for Different Purposes
Tag Material for Lockout Applications
23 September 2021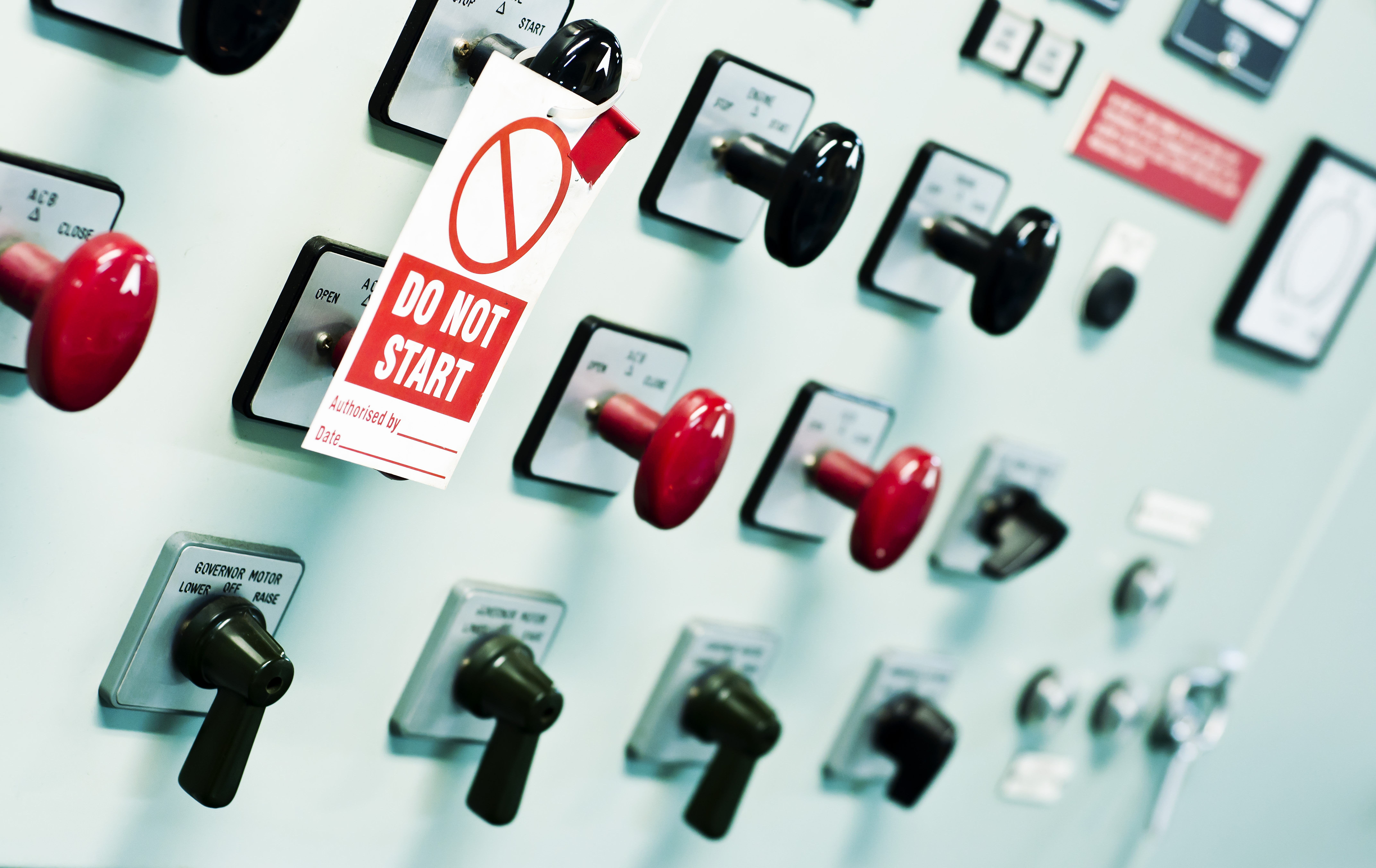
Tags
Recently I wrote an article about standardizing your materials before you begin writing your procedures: Standardizing Before Writing LOTO Procedures. I now want to get into more details by focusing on the tags you’ll be placing on the different types of machinery and components. I’ll explain why it’s important to properly choose your tag material.
What are your tags made of?
What’s the best material to use in the particular environment you’re in? If you’re in a fairly neutral, mild-temperature environment, you have the most options to choose from. But if you’re in a very hot, cold, damp, or corrosive environment, you must be very careful of your choices of tag and fastener materials.
Plastic tags are cheap and easy to manufacture. They are fairly durable but may not be able to withstand extreme temperatures. In that case you could go to a stainless steel or aluminum tag.
But what if there’s something acidic in the air? That could chew through the metal. We’ve seen that happen where the company spent thousands of dollars on metal tags and hundreds of man-hours to place the tags on all of their devices, only to have to replace them within a couple of years. The tags were fully rusted and illegible.
On the other end of the spectrum, mining operations in Northern Canada regularly see temperatures in the -50°C range. Plastic tags become brittle at those temperatures and easily break apart.
Tags need something to attach them to your equipment
You also need to be conscious of the fasteners. If you use plastic zip ties to hold tags to steam tubing for example, the heat from the steam will melt the plastic and the tags would fall off. That might not be a big deal normally, but in some places that can be dangerous.
A good example is a company that processes dairy products. If a fastener broke and a tag were to fall into the product, it would be a real problem, especially if those tags house germs. So, you would need tags and fasteners that don’t hold germs and are detectable. In this case, it’s a no brainer. Stainless steel. If a piece were to fall anywhere in the process, a metal detector at the end of the line could see and reject the unwanted metal parts.
A secondary problem with a fallen tag is that it’s going to take longer to find and confirm the right valve, disconnect, or piece of equipment. It’s not a huge problem, just a time waster.
Some facilities need more than one type of tag
Normally when you plan out a facility, you’re able to use the same type of tags throughout. But it is possible to have multiple environments within the same company, such as an ore processing facility.
One building could be extremely hot, while the next could have an extremely acidic environment. They even have areas that have a fine, black dust in the air, like flour. In that last area, the dust would cover the tags, making them illegible. One such company decided to use metal tags that had the letters and numbers bored right through. This way a worker could tap the tag against a wall to kick out the powder and be able to properly read it.
Size does matter
Will all of the tags be the same size for everything, or will they be a different size for each type of equipment? You might want to use a 10” x 10” tag because the numbers are so long. However, if the valve is half that size, it won’t make sense. if you have a machine that is 3 stories high, you might want a larger tag so it can be found easily.
The labor cost of putting tags on
Many companies don’t see the importance of choosing the most suitable tag material for their business. Let’s look at the costs of attaching tags. As a rule of thumb, you can place roughly 10 tags per hour (about 6 minutes each). If you have 1,000 valves and 500 pieces of equipment, you’re looking at 1,500 tags. Divide that by six, and you can expect to take about 250 hours to install all of those tags. And let’s say your employees are costing you $50 an hour. That’s $12,500 of manpower just to put the tags on.
Even though putting tags on equipment isn’t a huge cost, it is taking up your workers’ time. Time they could be making the company money. Planning the best tags and fasteners to put on your parts is worth the effort. Having to replace your tags every couple of years is a costly and disruptive process that can be easily averted by using the right ones the first time through.
Isn’t this Nitpicking?
Yes, I know. It does sound like we’re getting into extreme details. But some good planning from folks that have experience can save you a lot of headaches, wasted time, and added costs.
Your tag manufacturer/supplier is a great resource that would be happy to help you choose the best material for your application. If you would like a spreadsheet of tag material versus their applications, give CONFORMiT a call.