LOTO | Different Types of Locks for Different Purposes
The importance of confirming your power and fluid disconnect
8 March 2022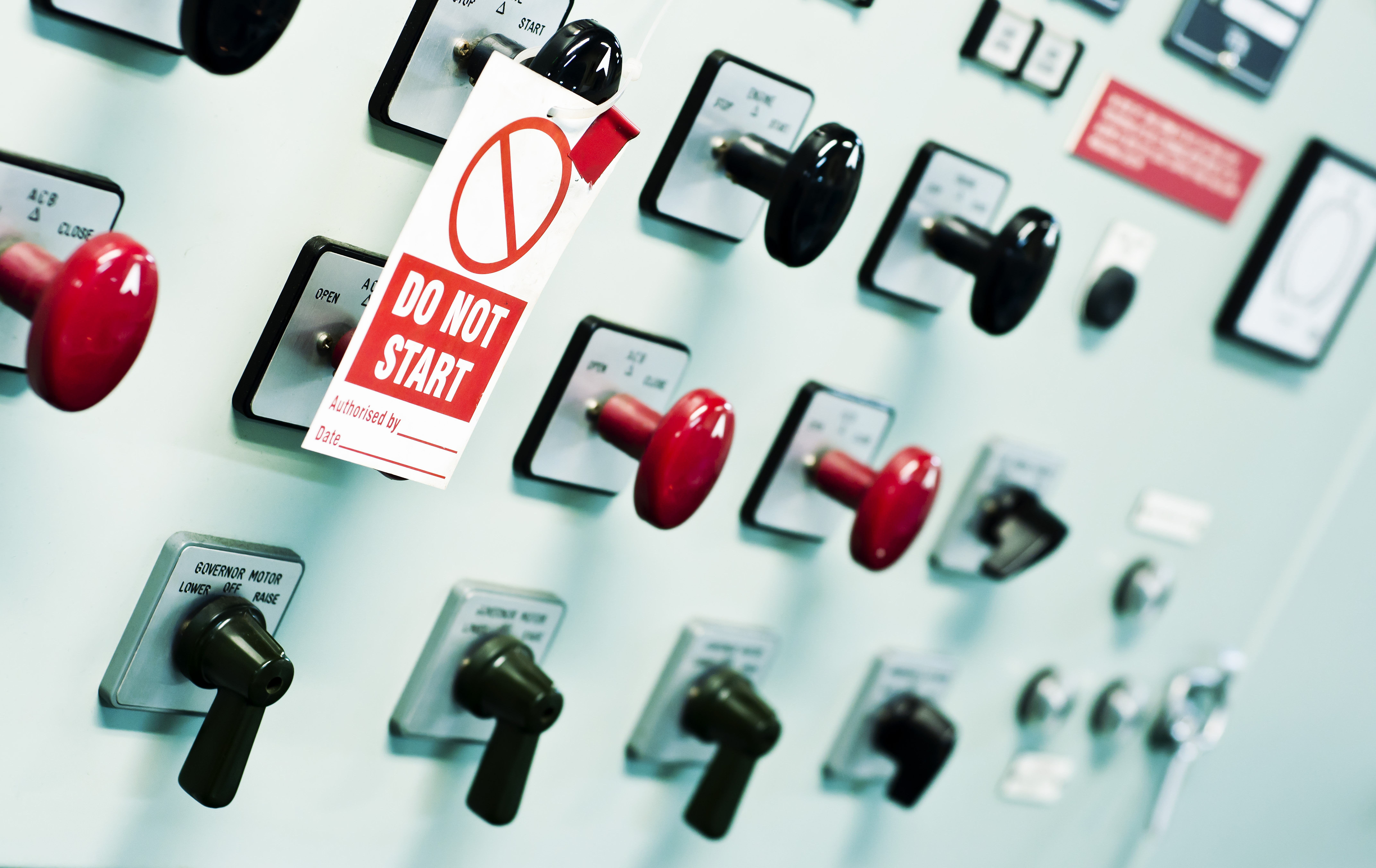
Disconnect Power and Fluid
Picture this, you’re in your living room about to install a new ceiling fan, but you must ensure the power is off first. So you have someone stand in the room with the light on while you run to the basement or garage where the breaker box is. Now you systematically try each breaker that has the potential to be the right one yelling after each one, “how about now?” until they yell back, “The light just turned off!”
Sounds familiar? Well, that’s quite often how large facilities verify that the power is off too. Someone will be standing next to the equipment with a radio while someone in a different room will try to start it.
The problem with this method is that it only covers one of the two reasons you should perform start-up tests or zero energy verifications as part of your lockout strategy.
1. Pulling the right breaker
For electrical power in a large facility, imagine that you walk into a room where there are 100 different electrical switches or breakers on a wall and they tell you to pull the one for the machine that’s halfway down the facility.
- First, you’ll check your procedure to confirm the correct one, using a unique identification code.
- After you pull the breaker, you will have to verify that the power is off.
2. Make sure that the breaker you pulled is doing its intended job
Now that you’ve confirmed that you’ve pulled the right breaker, you need to verify it’s not shorted, and not allowing any current to pass.
Most industrial, electrical disconnect switches use three phases. That means within your disconnectors; there are three knives. When you pull the breaker off, the knives come out of their brackets. But if one knife stays welded to its brackets, some electricity will continue to flow through that one phase. It won’t be enough to power your machine, but if you try and work on that machine with that much electricity still going through it, you’ll get a surprise.
The second method of ‘no power’ verification is necessary to be safe. It will depend on your setup but using a power meter to test for electricity, is a good method for most places.
You do a similar verification with fluid valves. Once you shut off the valve connected to your machine or tank, visual verification is the best. Not possible? You need to find another method of verification.
If your valve is faulty and lets fluid leak through, it can be unsafe for the maintenance worker. If it’s just water, it’s only a nuisance. But if it’s something toxic, the worker or others nearby can be injured.
The ISO standards tell you to verify the absence of energy or fluid leaks. Unfortunately, they don’t point out how, because there’s no single way to do it.
You want to get to a point where your company has standardized verification processes with all electrical power and fluid flow. If you are relying on people’s expertise to know which strategy to apply to each situation, make sure and write out those procedures for future workers.
Double Block and Bleed
In some high-risk cases, isolating the energy at a single point is not enough. When working with high severity fluids (highly corrosive, highly toxic, etc.), blocking the incoming fluid at two separate points and having something in place to bleed the line may be necessary to make sure you’re going to be safe when working on the machine.
Sometimes the fluid poses such a threat that you need to split piping junctions to install a blank (a full plate) to ensure the pipe is fully blocked. To do that, you have to split the joint between the pipes to install the plate. Is there pressure inside? Is there fluid inside? Which bolt do you loosen first? The one facing you – will you get splashed? The bottom one – are you at a height with possible people below?
If there were only one obvious way to do a LOTO, we wouldn’t need procedures. But that’s generally not the case. There are all kinds of different scenarios you could face; all needing a slightly different approach. Working out all of the finer points and creating procedures not only keeps your workers safe, it streamlines the process so you don’t have to figure it out each time.
Consider getting a professional service to work out optimum procedures. They will work things out based on what’s considered best practices and aren’t impacted by company opinions or politics. And they will be highly trained in these specific situations, which isn’t always the case with in-house workers.
Conclusion
The biggest reason to create procedures is for the future. You might have very experienced people doing your maintenance; people who can remember every step of every single procedure you have. But at some point, they will move on. As new workers come in, procedures or checklists can greatly reduce the training time and the need for trial and error, figure-it-out-on-their-own methods.
We can assume that these types of measures may seem over the top to some. Workers might want to cut corners to save time and money for their company. This is admirable, but it only takes one accident to lose all that ‘saved’ money, and more. To truly do what’s best for the company, follow the safety procedures and help improve them to get that perfect balance between safety and productivity.