How to Find EHS Solutions Built with Global Companies in Mind
15 August 2024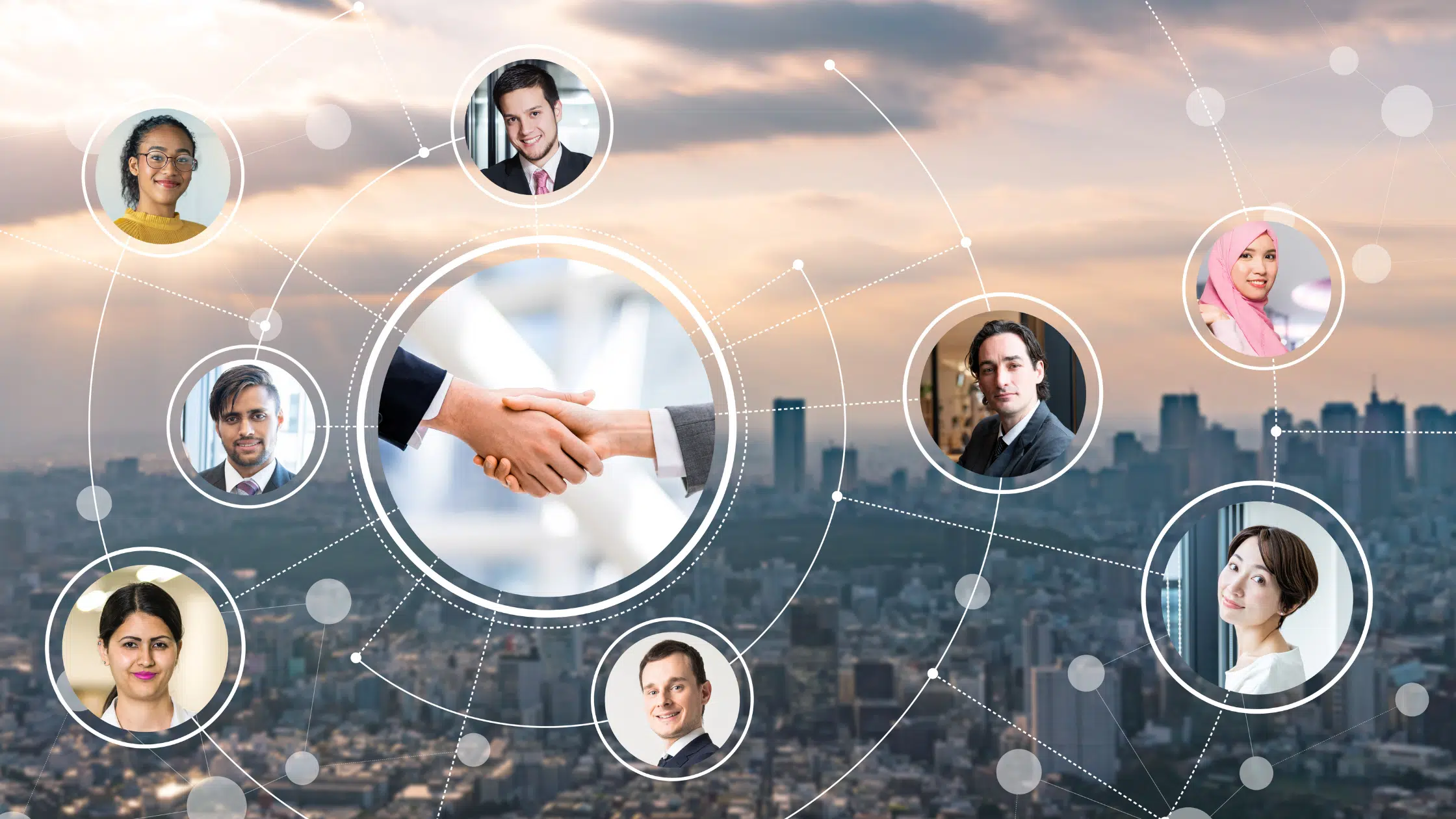
Do Multi-faceted EHS Solutions for Global Companies Exist?
A successful global company is founded on diverse individuals and cultural landscapes. With this beautiful diversity comes many challenges. You may wonder if a multi-faceted EHS solution, built with such challenges in mind, is available. If these global EHS solutions exist, are they reliable?
Consider the high-level variations—country to country—in production costs, wages, and market value. Think of day-to-day challenges—employees worlds apart, speaking different languages, trying to share knowledge to unify solutions and improve safety. Collaboration is no small feat for any multi-national corporation.
The Reality of Safety Challenges Associated with Global Diversity
A significant barrier to global EHS strategy is the same variety of languages and cultures that make a company great. Diversity leads to miscommunication and misunderstanding. In turn, inconsistent safety practices and accidents abound. Most operations managers, maintenance teams, and health & safety leaders are navigating their positions in less-than-ideal circumstances. “Creating successful work groups is hard enough when everyone is local and people share the same office space.” – Harvard Business Review.
Floor-level workers are trying to bridge gaps in processes, improvising just to complete the task at hand. Leaders want solutions, but integration is a pain and employees are reluctant to change.
If you are running multi-lingual teams in multiple locations, what is the solution for elevating safety protocol? For worldwide companies in high-risk industries, the importance of a unified approach to EHS cannot be overstated. A balanced combination of technology, cultural sensitivity, and strategic planning enables solutions that work for everyone, everywhere. The magic is in a solution that is flexible enough to adapt to local needs, and strict enough to maintain consistency across the board.
Shouldn’t Baseline Health and Safety Be Practiced Worldwide?
There are certain Environmental Health and Safety (EHS) obligations—rules, processes, regulations—that are generally accepted by all. For example, Personal Protective Equipment (hard helmets or steel-toed boots) is a basic component in employee safety protocol.
There is also the practice of “Due Diligence”, a.k.a. “Reasonably Practical”. “Reasonably practicable has been described by the Labour Program (Canada) as taking precautions that are not only possible, but that are also suitable or rational, given the particular situation. Determining what should be done is usually done on a case-by-case basis.” – CCOHS
While these standards seem simple and logical to employ, it’s not always the case. Weak safety culture and unregulated production is the culprit. Teams are trying to deliver quotas. If processes are not up to speed, or annoying to use, shortcuts seem like the best bet. Even with a new system, most teams struggle with implementation methodology. “Too often, hundreds of thousands of dollars in time and money go up in smoke because the…system is not functional.” – Ludovic Tremblay, Product & Industry Specialist, CONFORMiT.
Most general workers aren’t going to start lobbying for better methods, as they’re already juggling hierarchy and disruptions to production. Corporate doesn’t usually step in because of the difficulties of integrating new software and the headache of change management. The hassle just doesn’t seem worth the effort.
Why “One-Size Fits All” Solutions Don’t Apply
Material Measures
Beyond the basics, many protection methods may seem like no-brainers but aren’t readily available in some countries. Machine guardrails, for example, are a popular means of protection in developed countries. However, guardrails aren’t required in other parts of the world. While there is solid logic in using guardrails, the support isn’t there. Lack of pressure from regulatory organizations, tight budgets, and literally no access to the material itself is a problem.
Local Laws and Regulations
Consider laws and stipulations set out by local and federal governments. The ABCs of EHS safety in North America, for example, differ greatly from those of Europe or Africa. Not only do laws differ from place to place, but they also change—and in recent years, at an increased pace. As reported by the EHS Daily Advisor, “EHS professionals must foster a culture of continuous learning to stay ahead of regulatory changes and swiftly adapt their strategies to meet new compliance standards.”
Constant evolution creates a complex landscape for global companies to navigate, as they attempt to standardize safety protocols while conforming to local regulations.
Software Solutions
In addition to improving safety with tactile elements, regulatory constraints, and guidelines there is the component of technology.
Take the Paper Industry as an example. Each mill, within the same organization, is often at liberty to choose the software they prefer. As a result, a lack of quality control in safety protocol develops across locations. A lot is in play when companies consider increasing safety standards—safety is just one part of the equation and rarely is it the top consideration.
Decision-makers are forced to evaluate:
- Cost: Can we back up the cost of a solution with convincing data?
- Profit gain: Will we be able to deliver a significant gain in profit to ensure the software is sustainable?
- Ease of use: How much of a setback will employees face when integrating the new solution?
- Change management: How much pushback will there be in “switching things up”, and will employees comply?
- Mindset: Is the new solution too disruptive for legacy show runners?
- Safety: Will the software deliver, reducing/eliminating SIFs?
It’s wise to consider a software solution that has your exact pains and industry in mind. After all, you wouldn’t seek advice from your local car mechanic on how to fix one of your machines at work, and you wouldn’t ask your maintenance guy for advice on fixing your car. Both professionals may be the best at what they do, but that doesn’t mean they have the context or experience to take that expertise into other domains. If you are in the Pulp & Paper industry for example, make sure to seek experts that have experience solving your unique industry pains, that have spent quality time in mills, and know the full context of your environment. Cookie cutter solutions just don’t cut it when it comes to safety excellence.
By embracing these challenges head-on and seeking innovative solutions, global companies can lead the way in creating safer, more efficient workplaces for all.
Unique EHS Solutions Built with Global Companies in Mind
There is great hope that by sharing education and leading by example, these basic standards of safety will be adopted more and more by all. Multi-national companies can take the lead in maintaining a high bar for EHS, across their world wide locations. It takes a little consideration and planning, but overall if you find the right support you will bring your safety game to the next level.
For instance, one of our European clients in Mining & Metals, has sites all over the world. In working with us to tailor and develop the perfect solution for their Risk Management methods, Lockout Tagout included, they realized that the company as a whole would benefit from a unified system.
While each facility remains an individual business unit, we have connected them all on one single tenant, with vigorous cybersecurity from the ground up. Not only has this allowed their workers in North America to visualize and adapt their lockout tagout procedures, risk analysis, and inspections to those of their European counterparts, but they can do so in real-time, in their native language.
In addition to optimizing existing units, as they open new sites – anywhere in the world – their system is already configured to a corporate-approved environment. Managers simply tweak their settings to conform to facility-specific requirements and regional regulations.
Integrating their previous basic system (Word, Excel, and PDF) was a literal treat, as our innovative AI-powered technology imported and organized thousands of their ECPs in a matter of hours. They were up and running with a reliable and accurate system within a few days.
Imagine the Benefits of a Flexible, yet Fully-Reliable, Solution
Imagine you’re a maintenance supervisor working in the UK and you can reference your mines in Chile to adopt best practices and verify data—in English. The benefits of such unity go far beyond setup and day-to-day use of software. Imagine you’re a supervisor from Chile visiting a UK site in person. You can view files and execute tasks in your own language, within a familiar environment. Such a fine-tuned balance of congruency and flexibility brings your company an optimized level of control and efficiency.
Take a moment to really visualize what an EHS software solution, tailored to your unique needs, means for your site, your employees, and your company.
- The amount of data you can share in a connected system is priceless. As a global enterprise, with the correct rights and permissions – you can have immediate access to untold amounts of data. You can create, enforce, and maintain high-quality health & safety practices.
- As an overseers of an individual facility, you can aggregate shared data. Having the numbers to back up your EHS needs, requesting the resources from up top has never been easier.
- Standardization to control function and process ensures safety and swift on point action – regardless of your site’s location. Maintenance can easily manage and access previous ECPs and incorporate prior adjustments with context. Improving compliance alone, would relieve your company from costly and tedious fines, not to mention prevent near misses.
- Imagine facilitating cross-border communication and training. Platforms are tailored to account for your local cultural nuances, ensuring that safety protocols are both understood and respected by all of your employees, regardless of location.
- Not to be ignored is the ease of set-up for a new facility, regardless of it’s geographical location. Corporate-approved environments, pre-set roles and permissions, based in best practice, and minimal configuration for local laws would have you up and running in a flash.
The Road Ahead is Built on Sustainable Safety
Breaking down the barriers of language, country, and mindset doesn’t mean wreaking havoc on your operations. It’s about creating a unified approach that respects and accommodates the differences that make your global company unique. The end goal is to move the needle closer to 100% safety and 100% profit, and with the right tools and strategies, this is entirely achievable.
As companies continue to expand globally, the need for robust and adaptable EHS solutions will only grow. By leveraging technology, fostering a safety culture of continuous improvement, and remaining agile in the face of regulatory changes, you can exceed safety standards, ensuring the well-being of your employees and the success of your operations.
About CONFORMiT
For over 35 years, CONFORMiT’s Lockout Tagout system has been optimizing production, minimizing worker risks, and maximizing profits for high-risk industries across North America. Our zero-training-required, AI-powered enterprise solution frees employees from clumsy, chaotic processes. Unlocking safety excellence has never been so simple.
CONFORMiT enables its clients and their communities to provide a healthy and safe workplace while improving their productivity and profitability to build a more sustainable future.